Understanding Plastic Injection Molding Products and Their Importance in Modern Manufacturing
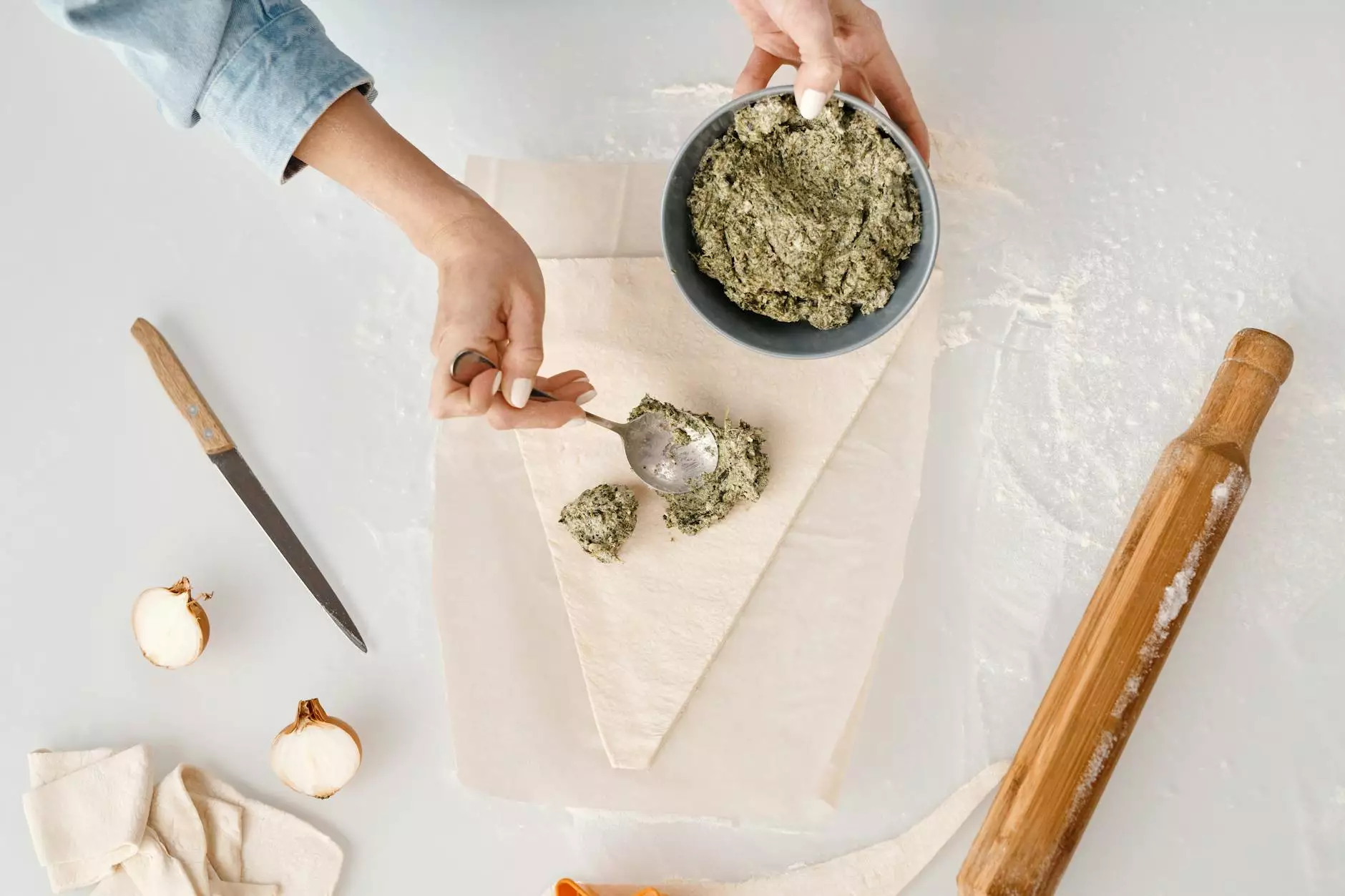
The world of manufacturing is vast and dynamic, embracing various methods that contribute to product creation in multiple sectors. Among these methods, plastic injection molding has emerged as one of the most significant processes, producing a vast array of products that touch our daily lives. In this article, we will delve deep into the realm of plastic injection molding products, exploring their applications, advantages, and the technology that drives them.
What is Plastic Injection Molding?
Plastic injection molding is a manufacturing process used to create parts by injecting molten plastic into a mold. This technique transforms raw plastic materials into precise and complex components. It is widely adopted in various manufacturing sectors, making it a cornerstone of modern production techniques.
The Process of Plastic Injection Molding
The injection molding process consists of several crucial steps:
- Material Selection: The process begins with choosing the right type of plastic. Common materials include thermoplastics and thermosetting plastics.
- Injection: The selected plastic is heated until it melts, then injected into a pre-designed mold under high pressure.
- Cooling: Once injected, the material is allowed to cool and solidify to take the shape of the mold.
- Demolding: After cooling, the mold is opened, and the finished product is ejected.
- Finishing: In some cases, additional processes are performed to finish the product, such as trimming or painting.
Advantages of Plastic Injection Molding Products
Plastic injection molding products come with numerous benefits that make them a preferred choice for manufacturers. Some of these advantages include:
- Efficiency: The ability to produce large volumes of products quickly makes injection molding highly efficient.
- Precision: Molds are crafted with high precision, allowing for the production of intricate designs with exact tolerances.
- Material Versatility: A variety of plastic materials can be used, including recycled plastics, which promotes sustainability.
- Cost-Effective for Mass Production: Once the initial mold is made, the cost per unit decreases significantly with larger production runs.
- Reduced Waste: The process generates minimal scrap material, making it an environmentally friendly option.
Applications of Plastic Injection Molding Products
The versatility of plastic injection molding products allows their use across various industries, including:
1. Automotive Industry
In the automotive sector, plastic injection molding is utilized to create components such as dashboards, door panels, and fuel tanks. The use of lightweight plastic not only reduces vehicle weight but also enhances fuel efficiency.
2. Consumer Goods
Many household items, from toys to kitchenware, are produced using plastic injection molding. This process allows manufacturers to create visually appealing and functional products in bulk.
3. Electronics
Plastic injection molding is essential in the electronics industry for producing casings, connectors, and insulation components, which help protect delicate electronic parts and provide necessary functionality.
4. Medical Devices
In healthcare, precision is vital. Products such as syringes, surgical instruments, and various medical device components often rely on the accuracy and reliability of injection molding processes.
5. Packaging
Plastic injection molding also plays a key role in packaging solutions. Products like containers, caps, and bottles are manufactured to meet rigorous safety and design standards.
Innovations in Plastic Injection Molding
The field of plastic injection molding has witnessed significant innovations that improve product functionality, production efficiency, and environmental sustainability:
1. Advanced Materials
The development of advanced plastic materials, including biodegradable plastics, enhances the sustainability of the injection molding process.
2. Automation
Incorporating robotics and automation in injection molding systems increases efficiency and reduces human error, making production faster and more reliable.
3. 3D Printing Technology
The integration of 3D printing with traditional injection molding allows for rapid prototyping, enabling manufacturers to streamline product development and test designs before mass production.
Challenges in Plastic Injection Molding
Despite the many benefits, there are challenges associated with plastic injection molding products that manufacturers must address:
1. High Initial Costs
The creation of molds can be expensive, which might be a barrier for small-scale manufacturers or startups.
2. Design Limitations
While injection molding is versatile, certain design features like undercuts can complicate mold design and production.
3. Quality Control
Ensuring consistent quality can be challenging, as variations in temperature and material can affect the final product. Rigorous quality control measures must be implemented to minimize defects.
Choosing the Right Plastic Injection Molding Partner
To maximize the benefits of plastic injection molding products, it’s essential to collaborate with a skilled and reliable manufacturing partner. Here are some criteria to consider:
- Experience: A partner with significant experience in injection molding can provide insights and ensure quality production.
- Capabilities: Verify that the partner has the necessary technology and resources to meet your specific needs.
- Reputation: Research their reputation in the industry through reviews, testimonials, and case studies.
- Customer Service: Good communication and support reflect a partner’s commitment to customer satisfaction.
Conclusion
The importance of plastic injection molding products in modern manufacturing cannot be understated. As industries continue to evolve, the role of injection molding will only become more prominent, driven by technological advancements and the demand for high-quality, efficient production solutions. Whether you are in the automotive, consumer goods, electronics, or medical device space, understanding and leveraging the benefits of plastic injection molding can lead to successful product outcomes that resonate with consumers.
For those looking to partner with a proficient manufacturer, DeepMould stands ready to provide top-tier services in plastic injection molding and metal fabrication, making it a reliable choice for your production needs.