Understanding the Role of Nickel Alloy Instrumentation Tube Fitting Manufacturers
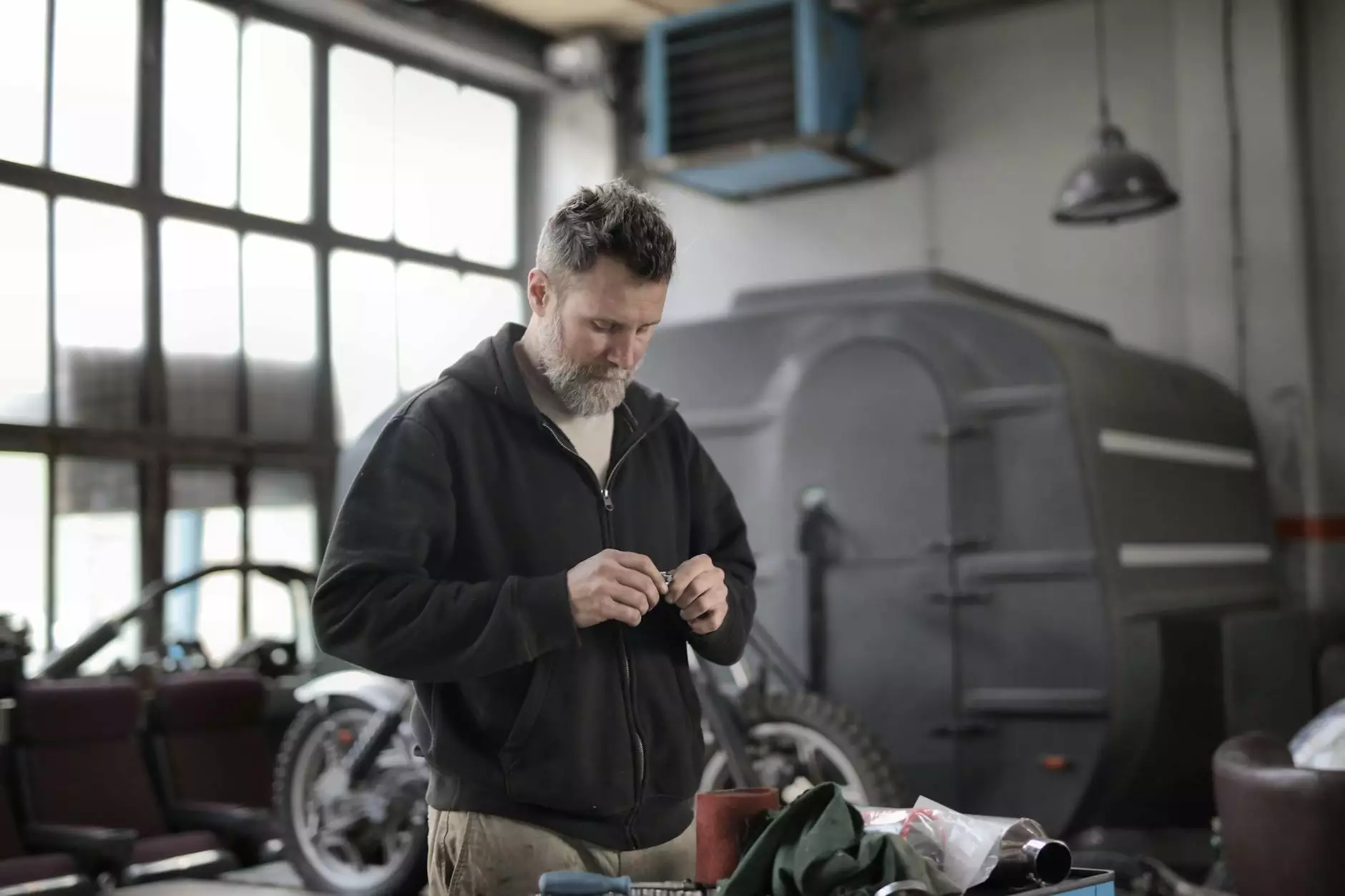
In today's fast-paced industrial world, the importance of high-quality fittings cannot be overstated. Among the many manufacturers in the market, the *nickel alloy instrumentation tube fitting manufacturer* plays a pivotal role in ensuring that industries can function smoothly. From oil and gas to pharmaceuticals, nickel alloy fittings are essential components that help maintain safety, efficiency, and reliability in various systems.
The Essence of Instrumentation Tube Fittings
Instrumentation tube fittings are crucial in controlling process flow and pressure in various applications. They enable a secure connection in fluid systems and are designed to withstand extreme conditions, which is where nickel alloys come into play. Known for their excellent corrosion resistance and strength, nickel alloys enhance the durability and reliability of tube fittings.
What Are Nickel Alloys?
Nickel alloys are metals primarily composed of nickel, accompanied by other elements that enhance their properties. The unique characteristics of nickel alloy include:
- Corrosion Resistance: Nickel alloys exhibit remarkable resistance to various corrosive environments, making them ideal for industries handling aggressive substances.
- High Temperature Performance: These alloys maintain their strength and integrity, even at elevated temperatures.
- Strength and Durability: Nickel alloys possess superior mechanical properties, making them a preferred material for critical applications.
Importance of Manufacturers in the Supply Chain
Manufacturers of nickel alloy instrumentation tube fittings, like samvayglobal.com, play a critical role in the supply chain. Their responsibilities include:
- Designing Innovative Products: Leading manufacturers invest in R&D to develop advanced tube fittings that meet the specific needs of clients, ensuring optimal performance.
- Ensuring Quality Control: High-end manufacturers adhere to stringent quality standards, thereby ensuring that each component can withstand the rigors of industrial applications.
- Providing Technical Support: Knowledgeable manufacturers offer support to clients in selecting the correct fittings for their applications, providing expert guidance.
Application Areas of Nickel Alloy Instrumentation Tube Fittings
Nickel alloy instrumentation tube fittings are widely used across various sectors, including:
- Oil and Gas Industry: Fittings are vital in exploration and production activities, providing reliable connections that withstand high pressures and temperatures.
- Aerospace: Lightweight and corrosion-resistant fittings made from nickel alloys are essential in aerospace applications where material performance is critical.
- Pharmaceuticals: In environments requiring high levels of cleanliness and sterility, nickel alloy fittings prevent contamination and ensure product quality.
- Chemical Processing: Nickel alloys are preferred for fittings that handle aggressive chemicals, ensuring safety and prolonging equipment life.
The Manufacturing Process: From Concept to Completion
Understanding the manufacturing process of nickel alloy instrumentation tube fittings provides insight into their value. The typical process includes:
1. Material Selection
The first step involves selecting the appropriate nickel alloy type based on the application's requirements, such as pressure, temperature, and chemical exposure.
2. Design Phase
Engineers use CAD software to create detailed designs of the fittings, ensuring precise dimensions and specifications to meet industry standards.
3. Fabrication
Once designs are finalized, the manufacturing begins. This stage often includes processes like:
- Machining: The material is cut and shaped using advanced machinery to achieve the desired dimensions.
- Welding: Components are welded together where required, ensuring strong and Leak-proof connections.
- Finishing: Surface treatments are applied to enhance corrosion resistance and aesthetics.
4. Quality Testing
Before shipment, each batch undergoes rigorous testing to ensure that the tube fittings meet safety and performance standards. This includes:
- Pressure Testing: Ensures that fittings can handle specified pressure levels without failure.
- Corrosion Testing: Evaluates the resistance of the fittings to various corrosive agents.
Why Choose a Nickel Alloy Instrumentation Tube Fitting Manufacturer?
The selection of the right manufacturer is critical for ensuring the longevity and efficiency of your industrial applications. Here are several reasons why partnering with a reputable *nickel alloy instrumentation tube fitting manufacturer* like samvayglobal.com is advantageous:
- Expertise: Established manufacturers have years of experience and a deep understanding of market needs, which translate into better products.
- Customization: Many manufacturers offer customization options to suit specific project requirements, enhancing overall performance.
- Reliability: Engaging with a reputable supplier ensures that you receive high-quality products delivered on time, minimizing project delays.
Conclusion
In conclusion, the role of a *nickel alloy instrumentation tube fitting manufacturer* is indispensable in various industries. These manufacturers provide essential components that ensure safety, efficiency, and reliability across a multitude of applications. By selecting a leading manufacturer like samvayglobal.com, businesses can be confident that they are using high-quality fittings tailored to their specific needs.
Whether in the oil and gas sector, aerospace, or pharmaceuticals, investing in nickel alloy fittings is a strategic decision that drives operational excellence. The expertise, innovation, and quality assurance provided by top manufacturers solidify their place in the industrial supply chain, making them invaluable partners for success.