Titanium Screw Manufacturers: Leading the Charge in Quality Fasteners
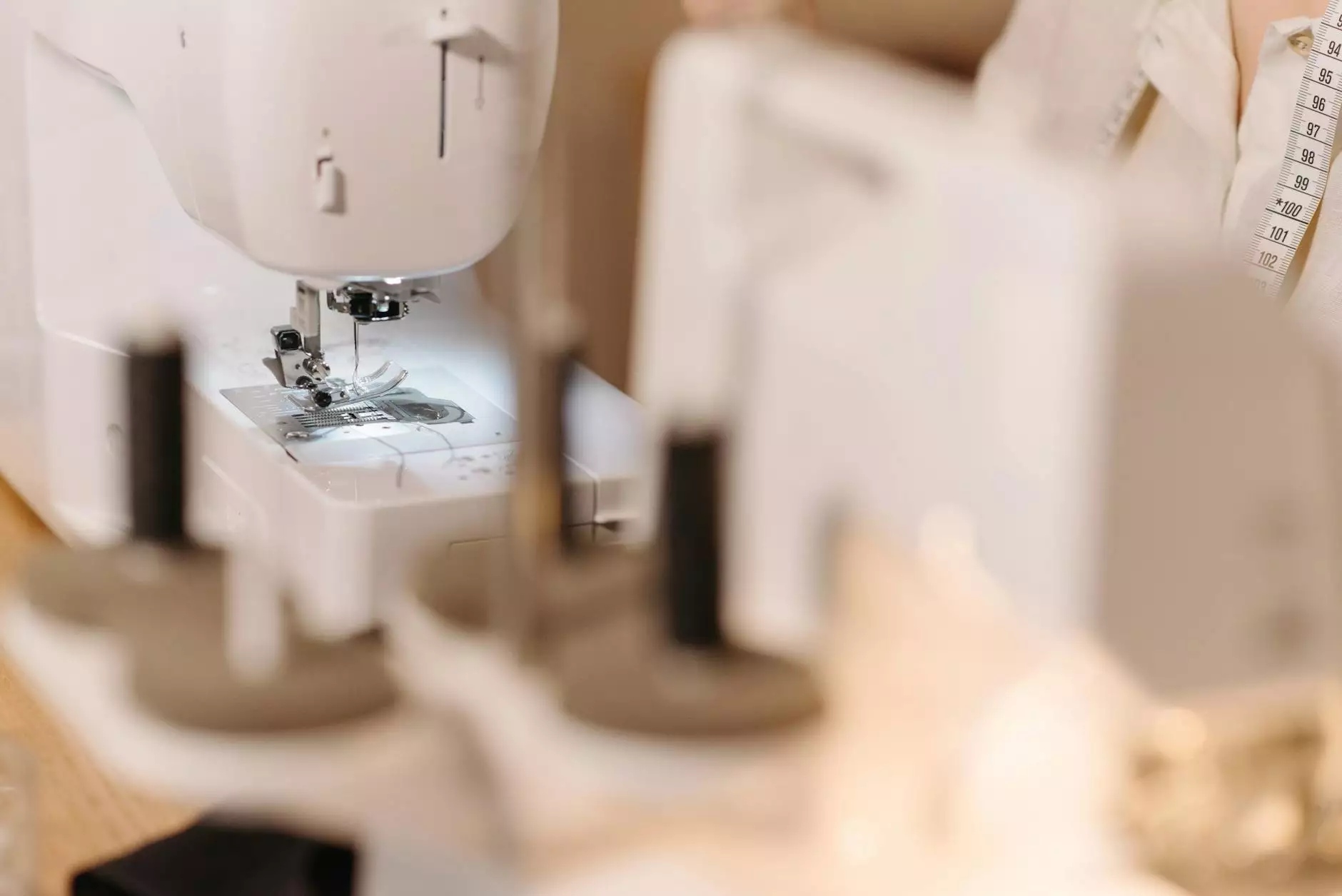
In the realm of manufacturing, titanium screws have emerged as a critical component due to their exceptionally high strength-to-weight ratio and superior resistance to corrosion. As industries strive for lightweight yet durable components, the demand for titanium fasteners is surging. In this comprehensive guide, we will delve into the various aspects of the titanium fastening industry, explore the benefits of titanium screws, and highlight some of the top titanium screw manufacturers, particularly focusing on titaniumbolts.com.
Understanding Titanium Screws
Titanium is a remarkable metal that has unique properties, making it an invaluable resource for manufacturers. Let's take a closer look at what titanium screws are and their significance in various industries.
What Are Titanium Screws?
Titanium screws are fasteners made from titanium, a metal known for its strength, light weight, and resistance to corrosion. Unlike traditional steel screws, titanium screws offer numerous advantages, particularly in environments where exposure to extreme conditions is common.
Properties of Titanium
- High Strength: Titanium has a tensile strength that can exceed that of steel, which allows for the production of screws that can withstand significant stress and strain.
- Lightweight: Titanium is approximately 45% lighter than steel, making it an ideal choice for aerospace and automotive applications where weight reduction is critical.
- Corrosion Resistance: Titanium's natural ability to resist corrosion extends its lifespan, offering durability even in aggressive environments.
- Biocompatibility: Titanium is non-toxic and well tolerated by the human body, making it a preferred material in medical applications such as implants and surgical fasteners.
The Advantages of Using Titanium Screws
The choice to use titanium screws over traditional fasteners is rooted in their numerous advantages. Below are several key benefits that make titanium screws a favorite among engineers and manufacturers alike.
1. Enhanced Performance in Demanding Conditions
One of the primary reasons industries prefer titanium screws is their ability to perform exceptionally in challenging conditions. In environments exposed to harsh chemicals, extreme temperatures, or marine environments, titanium screws maintain their integrity better than other metals.
2. Reduced Weight without Compromising Strength
The aerospace and automotive industries are particularly sensitive to weight. Every ounce counts towards fuel efficiency and performance. Titanium screws allow manufacturers to minimize weight while ensuring that components remain strong and reliable.
3. Long-Term Cost Efficiency
Although titanium screws may have a higher upfront cost compared to standard screws, their durability and resistance to wear can result in lower maintenance and replacement costs over time. This makes titanium screws a wise long-term investment.
4. Versatility Across Various Applications
Titanium screws are used in numerous applications, including:
- Aerospace (aircraft assembly and repairs)
- Medical devices (implants and surgical tools)
- Marine (boat construction and repair)
- Automotive (high-performance vehicles)
- Industrial machinery (heavy-duty equipment)
The Role of Titanium Screw Manufacturers
As the demand for titanium screws grows, so does the need for reliable titanium screw manufacturers. These manufacturers play a crucial role in the supply chain, ensuring that each component meets stringent quality standards and specifications.
What to Look for in a Titanium Screw Manufacturer
When choosing a titanium screw manufacturer, consider the following criteria:
- Quality Assurance: Ensure that the manufacturer adheres to rigorous quality control processes and is certified to international standards.
- Experience: Look for a manufacturer with a proven track record in producing titanium fasteners.
- Customization: The ability to provide custom solutions based on specific client requirements is a significant advantage.
- Technological Capability: State-of-the-art manufacturing processes and machinery indicate a commitment to quality and innovation.
Top Titanium Screw Manufacturers
Here are some of the leading titanium screw manufacturers in the industry, including Titanium Bolts.
Titanium Bolts
Titaniumbolts.com stands out as a premier manufacturer, offering an extensive range of titanium fasteners and screws tailored to meet various application needs. Their commitment to quality and customer satisfaction makes them a preferred choice for many businesses.
Other Notable Manufacturers
- Alcoa: A global leader in lightweight metals technology, Alcoa provides high-quality titanium products, including screws.
- Specialty Metals: Known for their extensive inventory of titanium fasteners, Specialty Metals specializes in high-performance applications.
- International Titanium: Offers a wide range of titanium products with a focus on aerospace and medical industries.
- Haynes International: A top-player with decades of experience in producing titanium and other high-performance alloy products.
Manufacturing Process of Titanium Screws
The production of titanium screws involves several intricate steps to ensure that they meet the desired specifications of strength, durability, and precision. Here is an overview of the typical manufacturing process for titanium screws:
1. Material Selection
The process begins with selecting high-grade titanium alloys. Grade 5 titanium (Ti-6Al-4V) is the most commonly used alloy in screw manufacturing, offering a perfect balance of strength and weight.
2. Forging and Machining
The selected titanium alloy undergoes forging to shape it into basic forms, followed by precision machining. This can include threading and cutting operations that define the screw's final shape.
3. Heat Treatment
Heat treatment processes are applied to enhance the mechanical properties of the titanium, ensuring the screws achieve the desired toughness and strength.
4. Surface Finishing
Surface finishing processes, such as anodizing or passivation, are applied to improve corrosion resistance and provide appealing aesthetics.
5. Quality Control
Finally, each batch of screws undergoes rigorous quality checks, including dimensional inspections and mechanical testing, to ensure they meet industry standards.
Future Trends in the Titanium Screw Market
The titanium screw market is continuously evolving, driven primarily by technological advancements and changing industry needs. Here are some trends that are likely to influence the market in the coming years:
1. Increased Demand for Lightweight Materials
As sectors like aerospace and automotive focus more on fuel efficiency and performance, the demand for lightweight materials, including titanium screws, is expected to rise.
2. Advancements in Manufacturing Technologies
Innovations in manufacturing methods, such as 3D printing of titanium fasteners, will enable more complex designs and reduce waste, making production more efficient.
3. Sustainability Initiatives
With growing awareness around environmental issues, manufacturers are seeking sustainable practices in sourcing and producing titanium products, focusing on recycling and reduced carbon footprints.
4. Expanding Applications
The versatility of titanium will lead to its increased use in emerging fields, such as renewable energy (solar and wind power) and advanced medical prosthetics, expanding the market for titanium screws.
Conclusion
Titanium screw manufacturers like Titanium Bolts are at the forefront of fastener technology, providing unparalleled products that meet the demands of various industries. With their strong performance characteristics, titanium screws are revolutionizing how we approach engineering and manufacturing. As industries seek stronger, lighter, and more corrosion-resistant fasteners, the role of titanium screws will continue to grow, shaping the future of manufacturing innovation.
Embrace the future of fastening solutions with titanium screws. For more information and high-quality fasteners, visit Titanium Bolts today!